How To Choose The Best Metal Finish for Your Shelter or Canopy
1. Introduction and Laws
Introduction
At Shelter Store, we pride ourselves on being a trusted supplier of high-quality outdoor solutions, including vehicle shelters, smoking shelters and sports shelters, bollards, and other street furniture. With a deep understanding of the unique needs of businesses, schools, public spaces, and local authorities across the UK, we strive to deliver products that meet expectations and serve clients for a long time.
One key aspect of our commitment to giving clients great products is understanding that every client has different needs. That is why we offer a selection of metal finishes to ensure the final product is high-quality, has a long lifespan, and aligns with your environment and aesthetic preferences. However, with so many choices available, selecting the best finish for your project can sometimes feel overwhelming. We have often found clients wondering what the best metal finish is for their specific situation.
To assist you in making an informed decision, we have created this comprehensive guide that explains the benefits and limitations of the different metal finishes we offer. Whether you want to protect your shelter from the elements or achieve a specific aesthetic, this guide will help you navigate the options and choose the best finish for your needs.
2. What Are Your Choices?
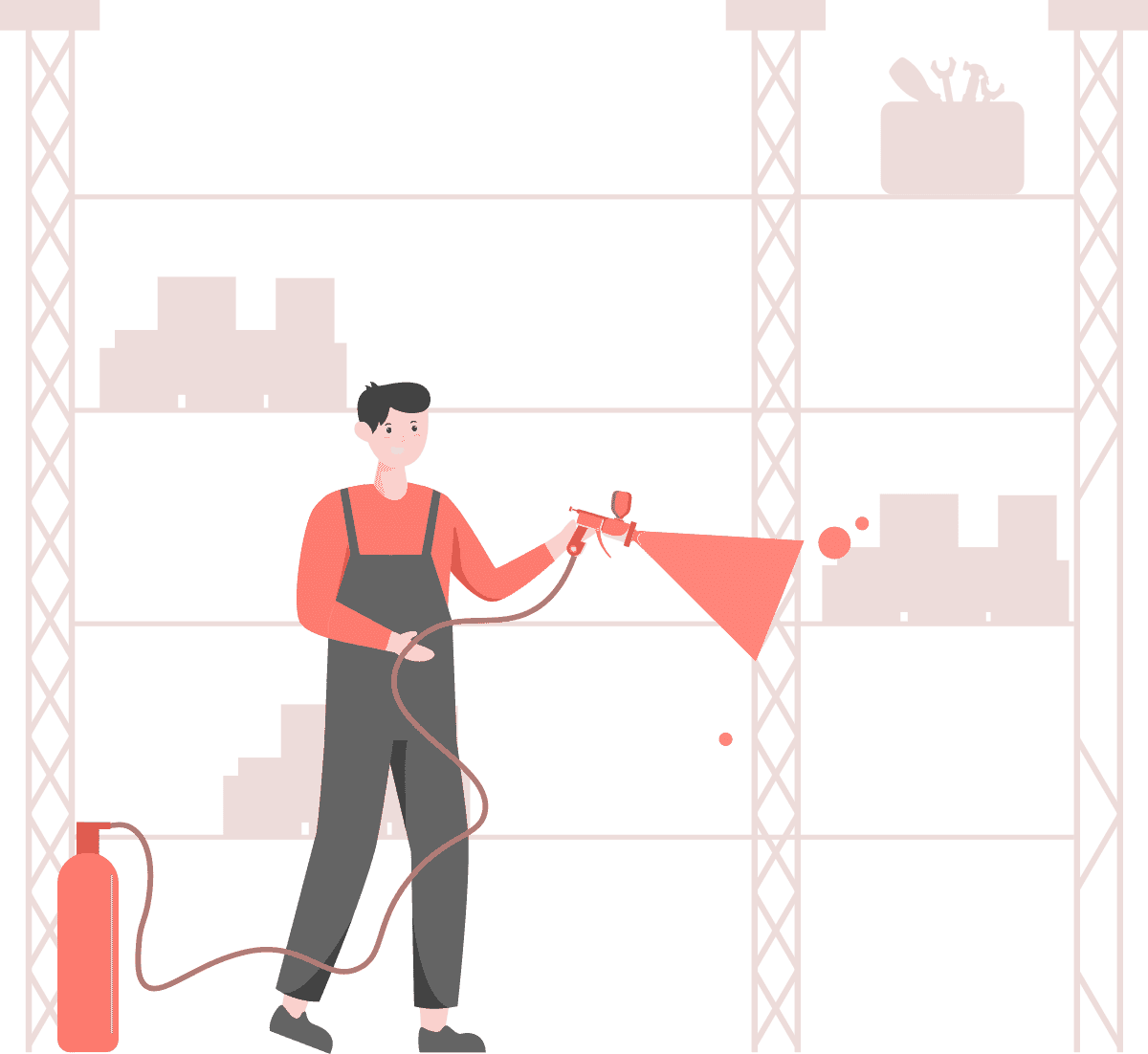
Steel is one of the most versatile materials, and it is used across sectors with a variety of finishes, like hot-dipped galvanisation, electroplating, powder-coating, phosphate coating, electropolishing, and many others. They serve different purposes. While some are used to reinforce the strength of the metal or protect against corrosion, others are primarily for decorative purposes, adding colour or a specific type of shine. Knowing more about the different metal finishes allows you to choose the most appropriate one for your next project.
So, what are your options? Here, we will focus only on the finishes we use and cover them one by one so that you know how they differ, what their pros and cons are, and how to care for them and the products they are used on.
Depending on the product you are looking at, there may be several options. For example, when it comes to our shelters – smoking, sports, bus, trolley, vehicle or waiting shelters, you can generally expect a sturdy steel frame, which can be ordered: as is with a powder-coated colour on the metal; you can have it galvanised; or you can select a combined option galvanised and powder-coated. Let's explore each of these.
3. Powder Coated Finish
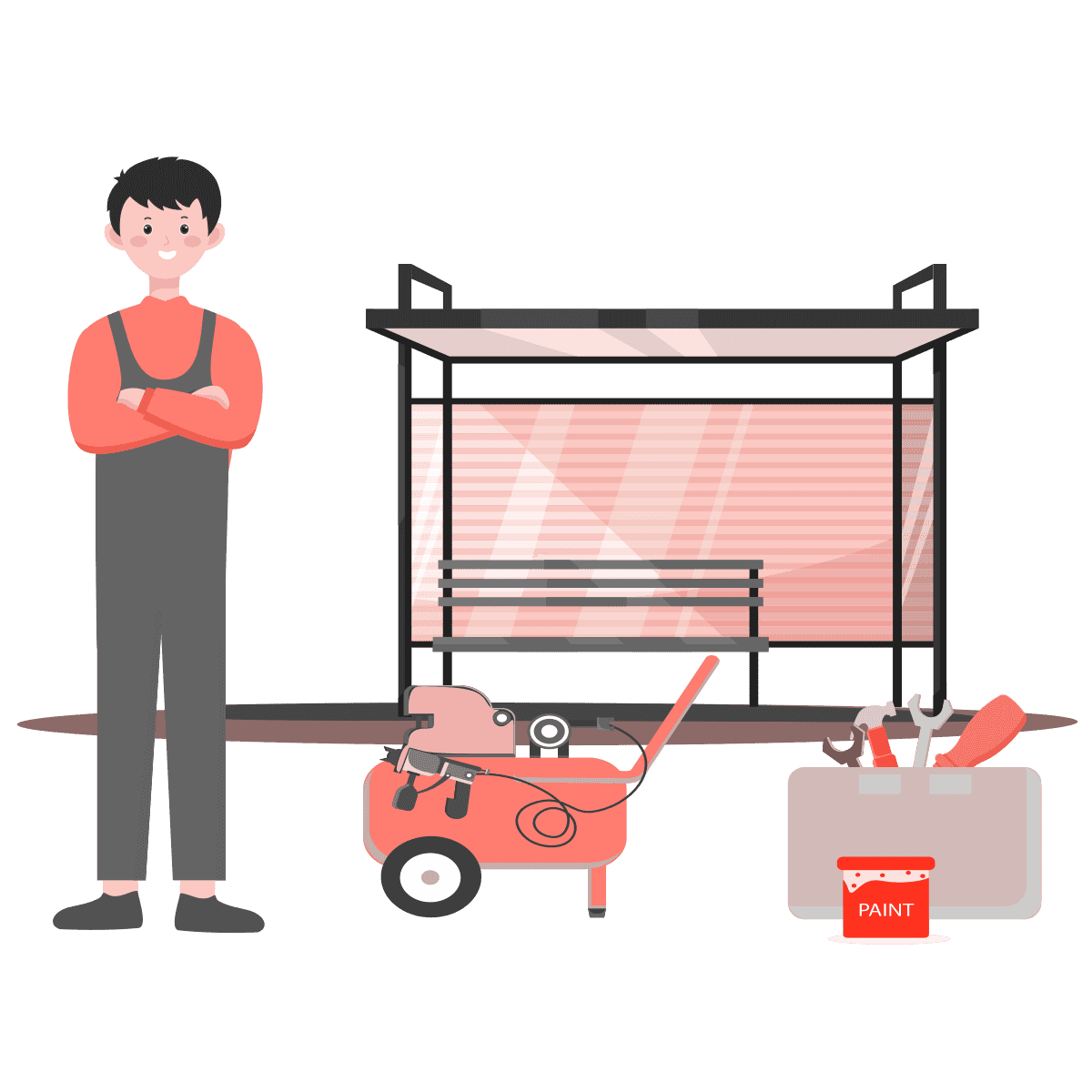
What Are the Benefits of Having a Smoking Shelter?
We will start with the powder-coated finish, which goes onto the raw metal once you have placed your order. This method is so popular and required by clients that we built our own in-house powder-coating facility to complete orders quicker and be in full control of the quality and process. Clients love customisation, and with the advancements in the industry every year, we are able to offer more colours, better paints, and better quality.
What is powder-coating?
Powder-coating is a dry finishing process that applies a durable, protective, and decorative layer to metal surfaces. Unlike traditional liquid paint, which uses a solvent-based formula, powder coating involves the application of a finely ground powder made from polymer resin, pigments, and other additives. This powder is electrostatically charged and sprayed onto the surface of the metal, which has been electrically grounded to attract the charged particles. The coated object is then placed in a curing oven, where the powder melts and forms a smooth, even, and hard finish as it chemically bonds to the metal.
We offer it on many of our products as an option because it allows clients to customise their shelter or bench with a colour of their choice. Modern paints, however, also have excellent qualities that make them efficient, providing the right aesthetic and decorative value and giving the metal extra durability and protection from the environment.
What are RAL colours?
Before we continue onto the pros and cons of powder-coating, we wanted to also cover RAL, which sometime buyers are unfamiliar with. RAL colours are the colours you can choose from when it comes to the powder-coated colour finish for your selected product.
RAL is a colour system, very much like the famous Pantone, which you may be more familiar with. It is a way of standardising colours, making it easy to communicate specific shades and consistently get the same colour results regardless of where the paint job is done. So, in short, RAL is a colour matching and management system used in powder coating to ensure standard colours are applied across the board.
Advantages of a powder-coated finish
Powder-coated products are very popular. They allow clients to add a personal touch to outdoor furniture, which can be made to fit the company's brand colours or blend seamlessly with the environment. Contemporary paints, however, go a step further and offer more than just colour.
Durability: Powder-coated finishes are known for their resistance to chipping, scratching, and fading. They provide excellent protection against wear and tear and exposure to environmental elements like moisture, UV rays, and chemicals.
Colour Variety: Powder-coating is available in a wide range of RAL colours. This allows clients to easily choose specific colours to match their design preferences, like brand colours or the architectural environment.
Environmental Protection: In addition to being visually appealing, powder coating acts as an extra protective barrier against rust, corrosion, and environmental damage.
Eco-Friendly: The powder coating process produces very little waste and is free from harmful solvents or volatile organic compounds (VOCs) found in traditional liquid paints, making it a more environmentally friendly option.
Cost-Effective: Since the process produces less waste and the finish is more durable, powder coating can reduce maintenance and long-term costs compared to other finishing methods. Additionally, ordering a product pre-painted saves you any extra spending post-delivery if you decide to paint it yourself.
Disadvantages of a powder-coated finish
Powder coating offers many benefits, but there are also some disadvantages to consider before you make a decision.
Extra Cost: Powder-coating is an extra step in the manufacturing process that requires preparation, equipment, and a curing process, so it comes at an additional cost.
Careful Application: Powder-coating is one of those processes that requires great attention to detail, which means that you need to be careful when choosing a provider. Firstly, powder-coating requires meticulous surface preparation. The metal must be thoroughly cleaned to remove any dirt, oil, rust, or contaminants, as these can prevent the powder from adhering properly and may lead to peeling, flaking or a defective-looking texture. The rest of the process – powder application and curing- must also be carefully followed for the final product to be high-quality.
Touch-ups: If a powder-coated surface is damaged (e.g., chipped, scratched, or worn down), repairing or touching up the surface may be a bit more tricky if you want to do it with the original powder-coating paint.
Galvanisation: One key thing to remember is that painting the metal does give it an extra coat of protection; however, the protective layer powder- coating gives you isn't as strong as the zinc layer, which is what you get from galvanisation. The tricky part is knowing that once a product has been powder-coated, it cannot be galvanised. To do so, you'd need to strip down the paint first. This is why it is very important to decide on galvanisation before you apply colour.
4. Galvanised Finish
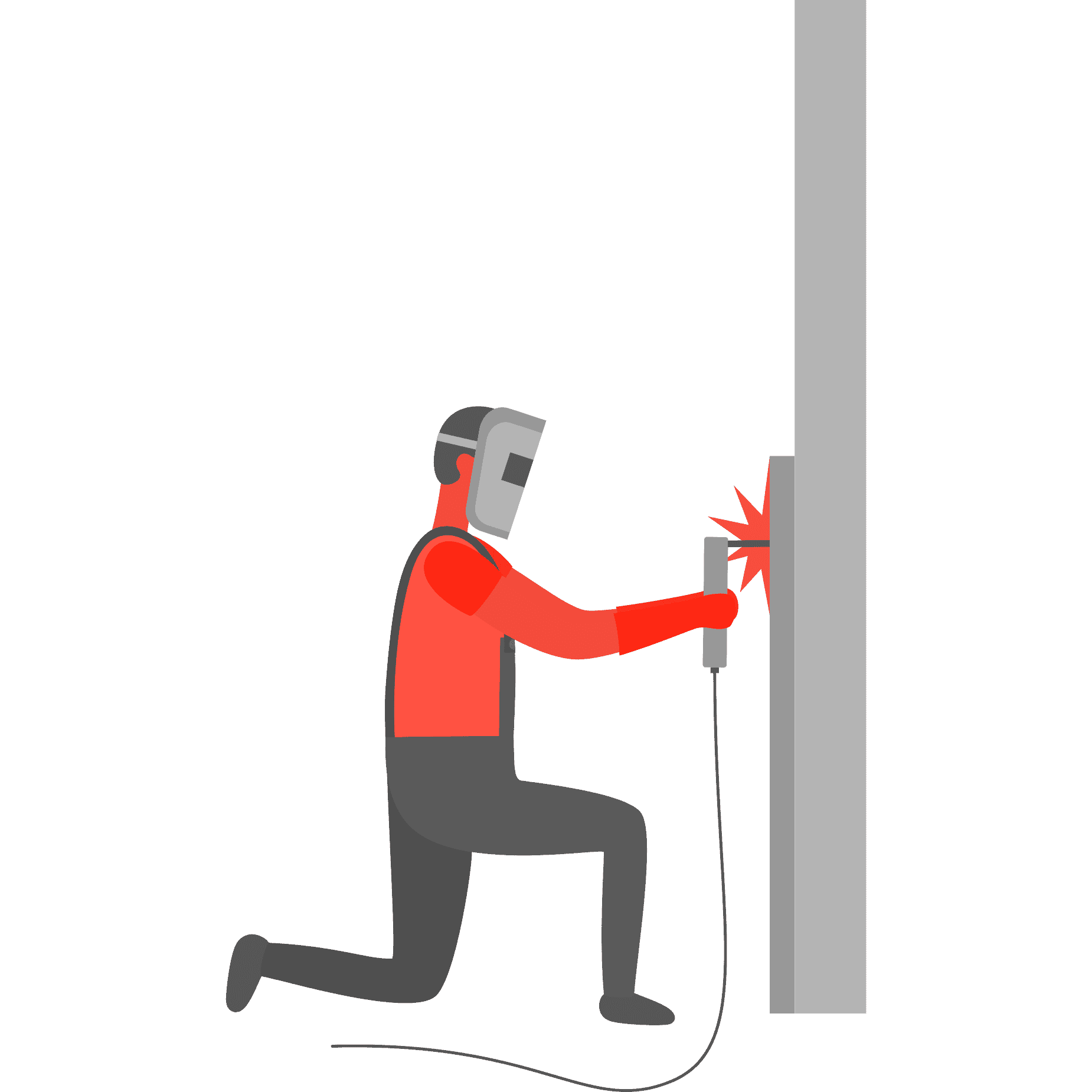
All of our shelters, and some of our benches and bollards and other street furniture are made of high-quality, sturdy steel. Steel is a great material to work with – it can be fully recycled indefinitely , has a long lifespan, requires little maintenance and is very strong. It is an alloy or iron and carbon typically mixed with other elements to add specific quality to the metal – like Chromoly steel, nickel steel or stainless steel.
Once steel is manufactured, it is often galvanised to give it extra qualities.
What is a galvanised steel finish?
Galvanising steel is a process that makes steel even stronger and more resistant to the elements. It is a protective coating applied to steel to enhance its resistance to corrosion and rust, primarily for outdoor or high-moisture environments. The process involves applying a layer of zinc to the steel surface. When the two bond, they create a barrier that protects the steel underneath it from exposure to environmental factors that cause rusting and degradation.
There are several methods to achieve galvanisation, but the most common one, and the one we use, is hot-dip galvanisation. With this method, the steel is submerged in a bath of molten zinc, allowing the zinc to form a metallurgical bond with the steel. This creates a thick and durable protective layer and leads to the typical mottled appearance on the surface due to the crystallisation of the zinc.
Hot-dipped galvanisation is our preferred method since it is cost-effective, leads to a nice and even zinc layer all over the metal and, most importantly, the zinc bath allows for typically weak spots to be covered well, too – like corners, recesses and seams, which often are the first to develop corrosion.
When deciding on your preferred finish, remember that galvanisation gives you a lot of added benefits.
Advantages of galvanised steel
Galvanisation is an added step and naturally a cost to the manufacturing of our products, but we always advise our clients to go for it if it is an option due to the numerous advantages it gives the metal.
Corrosion Resistance: Steel has iron as a main component, which makes it prone to rusting. This is a real issue that you need to mitigate, and the best way to do so is prevention—get the right product from the start. Galvanising a shelter is the quickest and cheapest way to extend its life, as galvanised steel has excellent rust resistance due to the zinc coating that goes on top of the metal. The protective layer stops moisture and oxygen from getting to the steel underneath.
Outdoor furniture, especially one that is used heavily, will inevitably get scratched or damaged over time. However, the zing barrier corrodes preferentially. What does this mean? The best thing about galvanisation is something called sacrificial protection —a process where when there are small breaks on the galvanised surface, the zinc surrounding them effectively sacrifices itself and corrodes first. This way, it protects the exposed steel, and even though some corrosion is happening, it is contained and slower, giving your products a much longer life.
Durability: The galvanisation process leads to a metallurgical bond between the zinc and steel layers. This coating gives the steel superior resistance to damage and makes it much more durable. The hot-dipped galvanisation process, on the other hand, as we mentioned above, is our preferred method of galvanisation. We like it so much because it allows the zinc to get into all nooks, corners and recesses, which are typically the weak points in every metal structure and where rusting begins. These little places are hard to protect from moisture, and they start failing over time, but the molten zinc bath allows them to be properly covered and gives them extra protection. That way, your metal product will have a longer life expectancy and require very little maintenance.
Low Maintenance: Galvanised steel is exceptionally low-maintenance due to its durable zinc coating, which acts as a protective barrier against corrosion. As we said above, even if scratched, the coating essentially self-heals by sacrificing itself before the steel rusts, ensuring longevity. This corrosion resistance makes it ideal for outdoor use, where it can last years without the need for repainting, recoating, or frequent cleaning, which reduces the need for repairs, inspections, and replacements.
Cost-Effectiveness: While galvanisation adds an extra cost to steel products, it is more economical in the long run because it extends the life of the steel and reduces maintenance costs. It is also a comparatively low price when stacked against other treated steels. Products made with galvanised steel aren't much more costly than their untreated alternative and can be used immediately after delivery without any extra costs being incurred.
Disadvantages of galvanised steel
Galvanised steel has few disadvantages aside from an extra cost, which could start weighing on the budget for extensive projects. However, the advantages and long-life properties usually outweigh the negatives.
Aesthetic Limitations: Galvanised steel has a very distinct look, with its splotches reminding of burst soap bubbles. It is very spangled and quite industrial, which may not suit all architectural designs or aesthetic preferences. There are cases where you may want to look into stainless steel for a sleeker and cleaner look.
Cost: Although cost-effective in terms of durability and compared with other treated steels, galvanised steel is more expensive upfront compared to untreated steel. You need to factor this into your considerations and budget.
Not Ideal for High-Saline or Acidic Environments: Again, there are some cases, other than aesthetic preferences, where you may want to look into stainless steel as opposed to galvanised steel. Galvanised steel can corrode quicker in environments with high salt content (e.g., coastal areas) or exposure to strong acids, making stainless steel a better option for such applications.
5. Galvanised & Powder Coated Finish
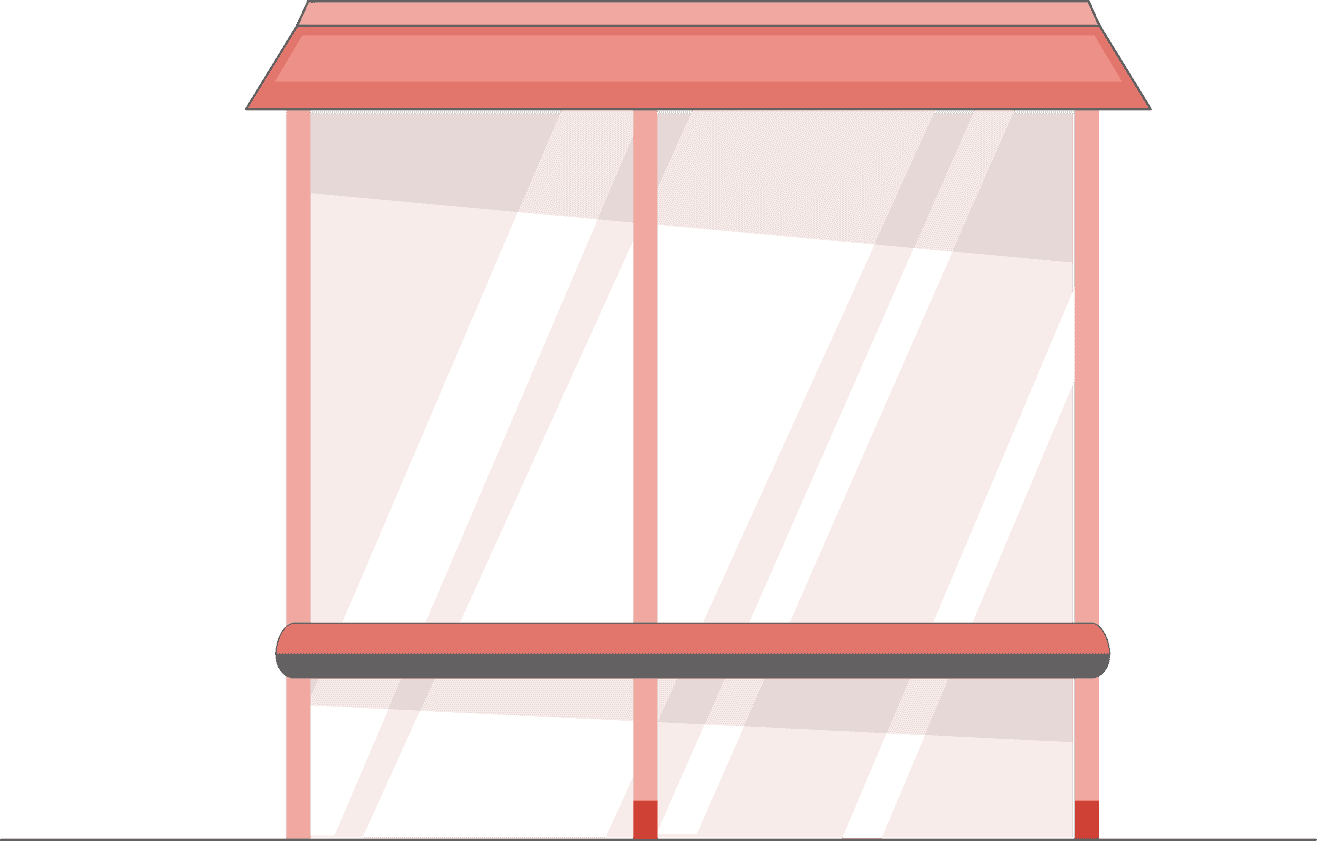
One of the options we offer on some of our products is a combination finish—steel that is both galvanised and powder-coated. This is the optimal choice as it gives you the added strength of metallurgically boned zinc and the look and colour of your choice.
The process of achieving this finish requires several steps. The key here is that the galvanisation must always be done before the colour. So, like with the regular galvanised finish, the product is submerged in a molten zinc bath. Once that process is finished and the steel has gotten its patterned look, the powder-coating can begin, followed by the curing.
Advantages of a galvanised and powder-coated finish
The combination of galvanisation and powder-coating gives the metal the best of both worlds. Galvanisation enhances steel's durability, strength, and resistance to rust and corrosion. It ensures long life and low maintenance.
The powder coating, however, gives it a beautiful colour finish in a shade of your choice and an added layer of protection. The paint coat effectively becomes an extra shield for the zinc, which in turn shields the steel. The cascading protection adds to the quality and strength of the metal, increasing its life even more.
Disadvantages of a galvanised and powder-coated finish
Choosing the combined option of the galvanised and powder-coated finish is a good choice that gives you a mesh of strength and design flexibility.
The main disadvantage is cost. Alongside that, the other thing you need to be careful about, which we already discussed in the section about powder-coating, is that you must be very careful when selecting a provider. The work needs to be done carefully and by a specialist. Painting instructions must be followed precisely to avoid any potential defects in the finished product. Lastly, maintenance may be needed with time, as the paint may need a little touching up.
6. Maintenance
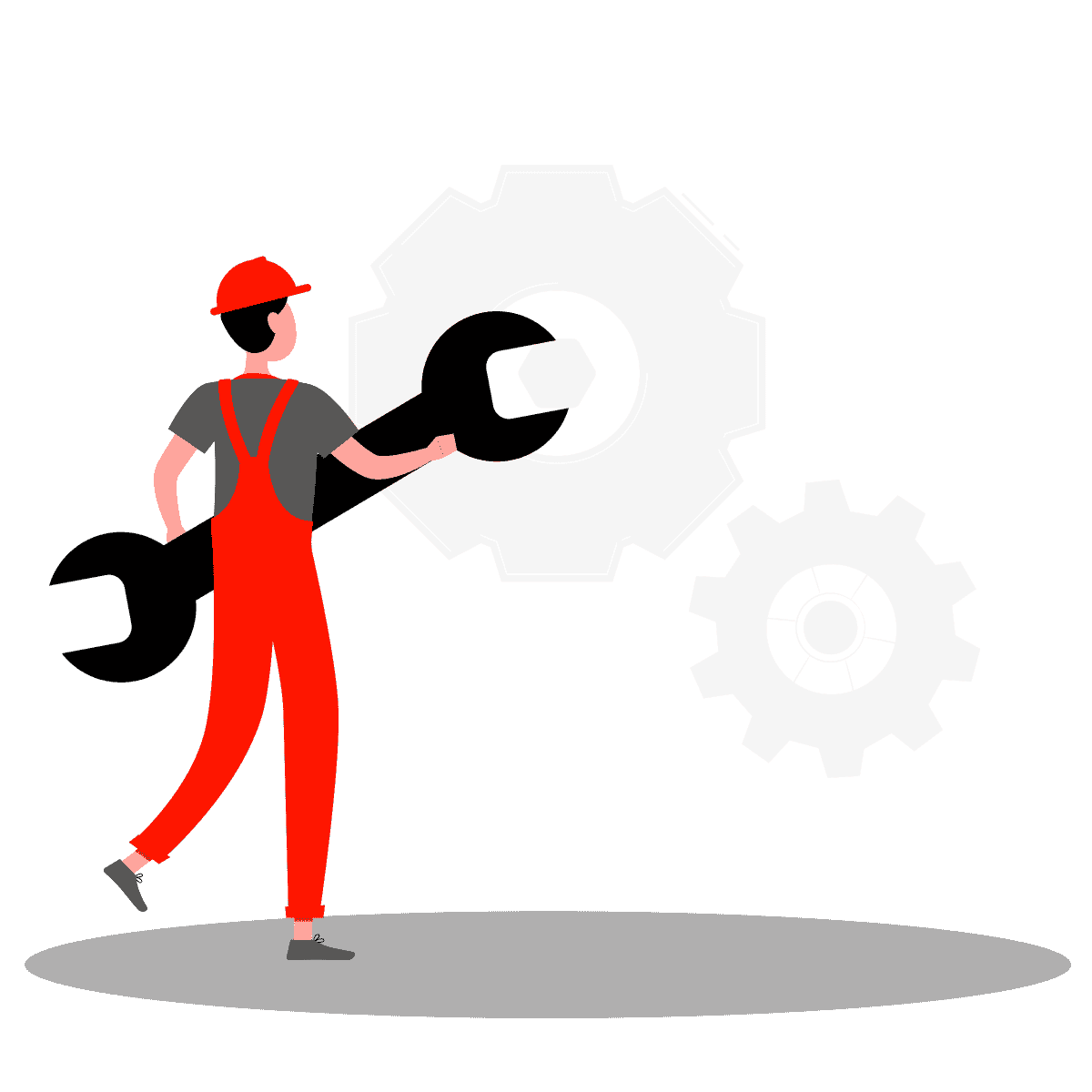
Proper maintenance is essential to ensure the longevity and appearance of outdoor metal structures. At Shelter Store, our products are designed to withstand various weather conditions and heavy use, but a little upkeep can go a long way in maintaining their quality. Here, we provide an overview of best practices for maintaining powder-coated, galvanised, and combined finishes to keep your outdoor shelters, bollards, and furniture in excellent condition.
Powder-Coated Finishes
Powder-coated surfaces are known for their durability and resistance to chipping, scratching, and fading. However, to ensure the long-term performance of a powder-coated finish, some basic maintenance is recommended:
- Regular Cleaning: Use a mild detergent diluted in warm water to clean powder-coated surfaces every 3-6 months, depending on environmental conditions. A soft cloth or sponge will remove dirt, dust, and grime without damaging the surface. Avoid abrasive cleaners, brushes, or harsh chemicals that could scratch or damage the coating.
- Avoid Scratching: While powder-coated surfaces are durable, they can still be scratched with sharp objects. Take care when moving objects around powder-coated areas, and address any accidental damage promptly to prevent rust.
- Touch-Ups: If the powder-coating does chip or wear down over time, it is advisable to touch up the damaged areas with a suitable matching paint. Powder-coating repairs require special care, so consult with professionals for any larger damages to ensure the surface is restored correctly.
Galvanised Finishes
Galvanised steel is specifically designed for outdoor durability, providing excellent protection against corrosion. This makes it a popular choice for street furniture and shelters. Although low-maintenance, there are a few steps you can take to keep galvanised finishes in top shape:
- Routine Inspections: Inspect the galvanised surfaces periodically, especially in high-use areas or harsh environments. Look for any visible signs of damage, rust, or corrosion. Small cracks or scratches should be addressed to maintain protection.
- Cleaning: Galvanised steel can be cleaned with a soft brush and a mild detergent. Avoid using aggressive chemicals that can strip the protective zinc layer. For stubborn dirt or contaminants, a mixture of warm water and vinegar can be effective without damaging the galvanised coating.
- Rust Prevention: In the unlikely event of surface rust, a gentle wire brushing followed by a zinc-rich paint can restore protection. This is particularly important in coastal areas or locations with high salinity, where corrosion risks are elevated.
Galvanised and Powder-Coated Finishes
Combining a galvanised layer with a powder-coated topcoat offers a double layer of protection and aesthetic appeal. Maintenance of this combination is straightforward but should be handled with care to preserve both finishes:
- General Cleaning: Clean regularly with a non-abrasive cloth, warm water, and a mild detergent. This prevents dirt and contaminants from settling on the powder-coated surface while preserving the galvanised layer underneath.
- Handle Scratches with Care: If the powder-coating is scratched, the underlying galvanised layer provides temporary protection. However, it is important to repair any noticeable damage to prevent long-term wear. Use touch-up paints that are compatible with powder-coating to maintain the appearance and integrity of the finish.
- Protecting Edges and Joints: Pay special attention to edges, joints, and corners, as these areas can be more vulnerable to damage. Ensure they are clean and well-maintained to avoid any potential rust starting in these spots.
By following these maintenance guidelines, you can significantly extend the life and appearance of your outdoor metal furniture and shelters. Investing a small amount of time in proper upkeep ensures that your products maintain their durability and aesthetic appeal for years to come, reducing long-term maintenance costs and the need for replacements.
At Shelter Store, we understand that selecting the right metal finish is crucial for creating durable, good-looking, and low-maintenance outdoor furniture and structures. Each finish—powder-coating, galvanisation, or a combination of both—offers unique advantages tailored to different needs, from aesthetic versatility to enhanced durability and corrosion resistance. Powder-coating provides a range of colour options for a customised look, while galvanised steel offers exceptional protection against rust and damage, especially in outdoor environments. Combining these finishes achieves the best of both worlds, maximising longevity and design flexibility.
We hope that this guide has simplified your decision-making process and ensured that you select the ideal finish that meets your project's functional and aesthetic goals. If you have any further questions, don't hesitate to get in touch. Our team will be happy to help!